Production Modules
Do you need an intermediate step between laboratory scale and large scale production?
Do you need to make small to medium quantities of specialist high value product?
If so, this may be the solution you are looking for.
Taking the skid mounted principle one step further, the Production Module approach simplifies the shipment, on-site installation and commissioning as far as practicably possible.
A Production Module consists of a process vessel mounted on a skid, along with all the ancillaries, pipework and control system to make it work.
Pilot grease kettle that is also an excellent unit to enable the customer to make small scale batches of high value specialist grease.
Closely emulating a full-scale vessel, this pilot plant does not have the consistency loss problem of lesser pilot plants
Gives the performance of a full-scale vessel in miniature and is easy to clean
- Batch Temperature to 220°C
- Pressure Range: Vacuum to 10 Bar(g)
- Contra-Rotating Agitation with Bronze or PTFE Scrapers, with the option of a bottom end disperser
- Fully Controlled Heating and Cooling Rates with Data Logging
- Dilution Oil Tank
- Vacuum Pump for De-Aeration
- Includes Product Pump and Toothed Colloid Mill
- Can be built with capacities from 25 – 100Kg
- 304 Grade Stainless Steel Contact Surfaces, with the option of 316 Stainless Steel
- Fitted with forklift sockets for easy handling
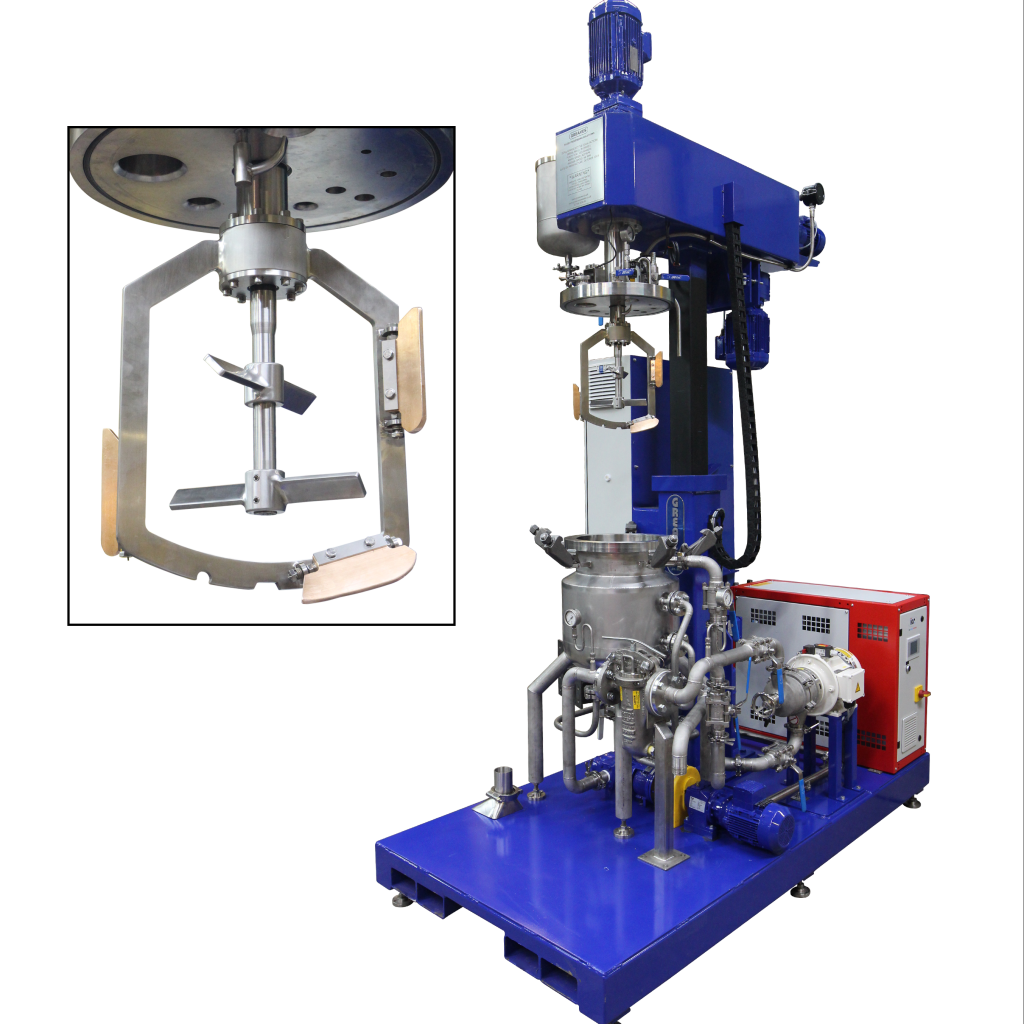
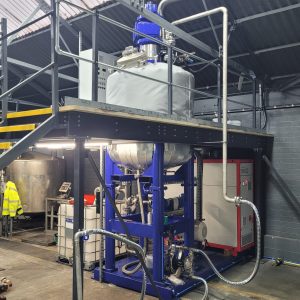
1 Tonne Food Grade and Specialist Grease Kettle module that was developed to allow the customer to make 1 pallet of complex, mixed soap or single soap grease per batch. It is built from 304 Grade Stainless Steel and is fitted with triple action agitation that includes a bottom end disperser to ensure that complexing acids do not accumulate at the bottom. The disperser also creates a milling action. The Kettle has a side and bottom jacket and is capable of running from full vacuum to +1 bar pressure.
The module is based on a skid that also holds the product pump, mill and thermal oil heater. A cooler is connected externally to the heater and the fume extraction is located as a separate module outside the building. The customer supplied mezzanine floor holds the vacuum pump for batch de-aeration.
Features include:-
- Batch Temperature to 220°C
- Pressure Range: Vacuum to 1 Bar(g)
- Contra-Rotating Agitation with Bronze or PTFE Scrapers and Bottom End Disperser
- Fully Controlled Heating and Cooling Rates with Data Logging built into the Control Panel
- Optional Dilution Oil Tank
- Vacuum Pump for De-Aeration
- Includes Product Pump and Toothed Colloid Mill
- Can be built with capacities from 1 – 2 Tonnes
- 304 Grade Stainless Steel Contact Surfaces, with the option of 316 Stainless
- Skid Mounted and the leg length can be adjusted at the design stage to suit the mezzanine floor height
For non-melting, clay-based greases where heat is not required, the Bentone Grease production module is a cost effective solution. This incorporates a 2 Tonne skid mounted unheated contra-rotating mixer, product pump, filter and in-line mill.
This module fitted into a 20 Foot Shipping container with the mixer laid horizontally and the access platform disassembled.
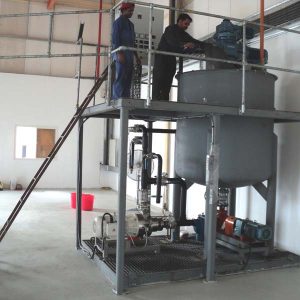
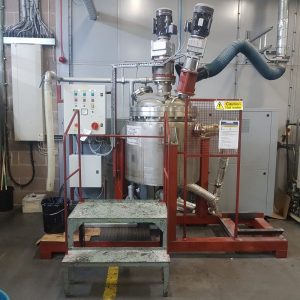
In order to meet the needs of a customer with a limited budget, this is a 250Kg Lithium Grease production module based on a re-purposed vessel that was modified to take an anchor and incorporator. This incorporates a 250Kg double motion jacketed atmospheric kettle, product pump and electrically powered thermoregulator.
The electrically powered thermoregulator, originally designed for the injection moulding industry, is a particularly effective option for heating and cooling small process vessels. It circulates thermal oil, which it can either heat with a built in electrical heating element, or cool, by passing the thermal oil through an inbuilt heat exchanger to transfer the heat to water.
A single panel with inverter drives and a temperature controller controls the entire module.
The unit was delivered to site on a flat bed lorry with the gear motors removed.