Powder Transfer by Vacuum
Surprisingly large and advanced manufactures in the process industry still physically empty bags and kegs of powders into process vessels via the manway.
This often creates a dust cloud that either contaminates the factory or gets drawn up into the vessel’s fume extractor, coating internal surfaces and clogging up the system. This is worse in heated vessels, where vapours can combine with the powder to form a cake.
Are you still tipping powders into your process vessel via the manway? We provide an easier, cleaner and safer option.
How It Works
The system is comprised of:
- Suction hose – The operator dips this into the container of powder and hoovers up the powder in the same way as using a domestic vacuum cleaner.
- Mancunian Head – This separates the powder from the air using a cyclone. The powder drops into the vessel, while air exits through the centrally mounted port.
- Reverse Jet Filter – The small percentage of powder that gets through the system is trapped and recovered here.
- Vacuum Pump – This generates the required suction.
- Exhaust to outside the building.
As shown in the diagram.
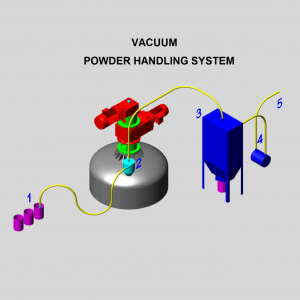
Used in grease manufacture since the 1970’s
In the 1970’s Jet-Lube Lubricants Ltd in Maidenhead, UK., were expanding their manufacture of oilfield thread compounds. These compounds use a combination of grease and powders, the latter prevent metal-to-metal contact between drill pipes, rods, casing and tubing.
The powders included copper, zinc and lead. This raised a health and safety concern of harmful and potentially toxic dust clouds being inhaled by the operators. To remedy this, Tom Ryland, the Managing Director introduced the vacuum handling system to all the oilfield compound mixers. The manufacturer also removed lead from the formulae in the 1990’s on environmental grounds.
The system ran for over thirty years with lead levels in the annual blood tests remaining consistently within safe limits. The only significant upgrade to the system was replacing the manually shaken filter unit with an automatic reverse-jet filter.
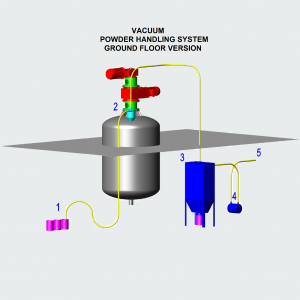
Do I need a vacuum rated process vessel?
No. Even though your process vessel (or vessels) will be at a negative pressure, the vacuum level will be very low.
However, if you have D-Lid access manways, like the one on the finishing kettle pictured on the right, you will need to install draught excluder style foam sealing round the lid edges to minimise the leakage. Of course the piano-hinge will pass air, but not enough to weaken the system.
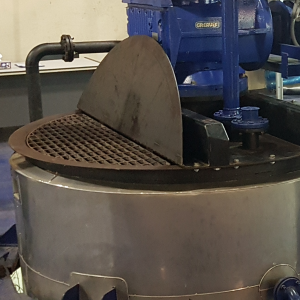