GREASE WORKER FOR IP50 and ASTM-D217
This is for an ASTM/IP standard test used in grease manufacture quality control. It is used to mash (work) the grease prior to testing its consistency (thickness) using a cone penetrometer.
The grease is loaded into a cylindrical cell and then the top assembly pushes a perforated plate up and down in the grease to break down any non-permanent gelling that may have occurred, which would disappear during the grease’s use. Most tests are done with 60 strokes, but occasionally, 10,000 or 100,000 strokes are done to investigate whether the grease hardens or softens during its service life.
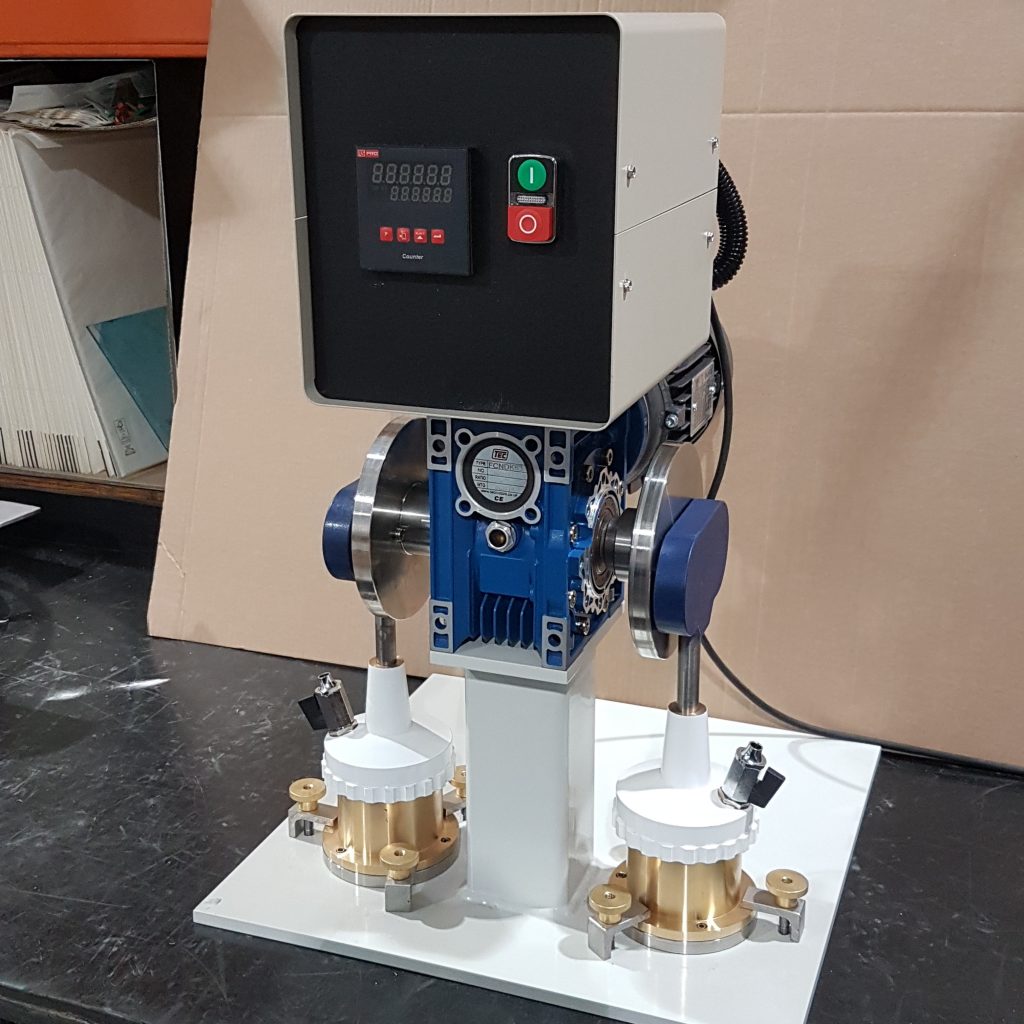
PASSPORT TESTING MACHINE
A major currency printing company approached a local engineering company for a quote on a passport testing rig. The engineering company approached us to provide the electronic control system and stepper motor drive. We ended up providing two of these systems.
This is a page-turning machine that flexes a page back and forth, as one of a series of rough-handling tests. This is to ensure that passports do not deteriorate unacceptably during their lifetime. These machines have been supplied in the UK and in the Mediterranean region.
UPGRADING A 1960’S SHELL 4-BALL TESTER TO VARIABLE SPEED
4 Ball Machines test grease under extreme pressure up to and beyond the point of failure. Tests include ASTM D-2596 for weld point and ASTM D-2266 for wear rate.
A grease manufacturer in the NW of England needed to carry out Weld Point and Wear Scar tests at a variety of RPM’s, rather than just at the industry-standard 1,500RPM.
This could be achieved by either buying a new 4-Ball Tester or modifying the original machine. The machine was mechanically in good condition but the electrical system had deteriorated significantly.
Our solution was to:
- Replace the single phase drive motor with a 1.5KW three phase unit
- Add a variable speed inverter to drive the motor and program it to respond in a similar way to the original motor
- Install a tachometer on the motor shaft to read and display the RPM
- Add a simple controller and data exporter that would shut off power at the weld point and also transmit RPM vs shaft revolutions via USB to a computer
The result was a 4 Ball tester with two additional capabilities. One was the variable speed and the other was the data acquisition capability
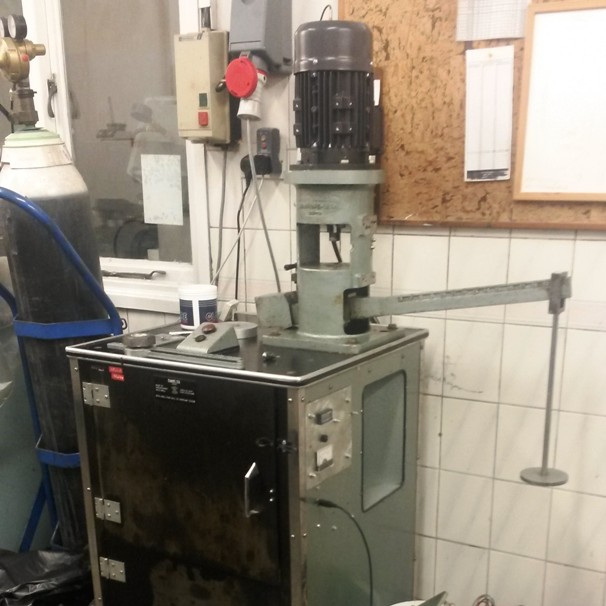