CHANGE-MAKERS, SPECIALISING IN PROCESS PLANTS FOR THE GREASE MANUFACTURING INDUSTRY
FLUID INNOVATION FOR A SUSTAINABLE FUTURE
At Ryland Research, we believe responsible innovation is about offering tailored solutions over one-size-fits-all approaches to empower industry leaders to innovate with confidence while keeping efficiency, sustainability, and quality at the core.
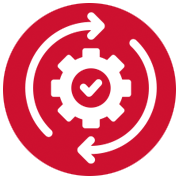
MORE EFFICIENT
PLANTS & EQUIPMENT
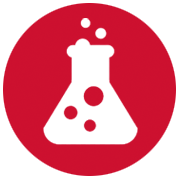
ENHANCED
FORMULATIONS
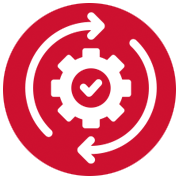
REDUCE ENERGY COSTS
AND CONSUMPTION
FUTURE-READY GREASE PLANTS
Designing a new plant or upgrading an existing one? We create tailored, efficient solutions that streamline production, minimise waste, and scale with your business—so you stay ahead in a changing industry.
BALANCING EFFICIENCY WITH SUSTAINABILITY?
Our waste heat recovery and fume management solutions help you cut costs, lower emissions, and meet regulatory standards—without compromising performance.
STRUGGLING WITH FORMULATION CONSISTENCY?
We provide expert review, refinement, and validation, ensuring your processes deliver maximum efficiency, quality, and reliability.
ENHANCING SAFETY, REDUCING RISK
Protecting your team starts with the right processes. We identify hazards, streamline operations, and recommend smart upgrades to improve workplace safety and compliance.
EXPERTISE BUILT OVER DECADES
For more than 30 years, we’ve helped companies around the world design and build equipment for manufacturing high-performance lubricating greases. We’re passionate about engineering smarter, more effective solutions, whether that means using cutting-edge technology or finding clever ways to do more with less.
We don’t just provide plant and machinery, we also help clients develop and refine grease formulations, from mono-soap and complex blends to non-melting types, for all kinds of uses.
From the blog
Process Upgrading or Changing – Can it Cause Unexpected Changes to the Product?
Sometimes it is necessary to change processes to improve productivity. However, there is a concern that the finished product may look different to the customer, even if the performance is
Automating process plants – common mistakes and how to avoid them
The Fears “Can we use this?”, asked the client when pointing to the two grease kettles during a recent commissioning visit, “without using this?”, when pointing to the two control
What can possibly go wrong?
You can anticipate most technical and financial problems that could arise in an engineering project, but there can also be the totally unexpected ones that trip you up later. Here
Commissioning visits – what we have learnt
If we were asked; “What is a typical commissioning visit like?”, we would be tempted to reply; “There is no such thing as a typical commissioning visit”. Although there are